Each fan has only one design point which is established
by a specific air flow, total pressure, air density,
and fan speed. Starting with these data, it is possible
to determine one planform and the twist distribution
which will accomplish the required work with minimum
horsepower.
To move air, the fan must
overcome two resistances, which are measured as pressure
drops across the fan. The first is a parasitic loss
called the velocity pressure loss and this is the energy
required to move the required air quantity without doing
any work to overcome the system resistance. Work is
done however to move the hot air away from the equipment.
The second resistance is
the static pressure loss. It is the accumulated losses
due to inlet louver, fill, drift eliminator, and fan
inlet pressure drop, etc. This would be the work to
be accomplished and reflects the design of the total
system. Whether the air is distributed evenly across
the fan is primarily a function of the blade and hub
design. A properly designed blade will have adequate
chord width and twist to ensure an even distribution
of velocity pressure over its entire length. A properly
designed hub will include a center air-seal disk which
prevents negative air flow into the center of the fan.
Following are two cases that most everyone has faced;
- Designing a new tower
from sketch, attempting to get the best design possible.
- Replacing a fan on an
old tower where practically nothing is known.
What we are seeking in the
brand new selection procedure is an optimum fan diameter,
number and type of blades, required pitch angle, fan
rpm, and some estimate of horsepower. In some cases
we are looking for an estimated sound-pressure level
to satisfy EPA requirements for working area noise levels,
more importantly noise level at a plant boundary, or
a given noise sensitive location such as a residential
area.
A problem that arises frequently
is a fan replacement for an old tower that practically
has no design data available. In this case, the only
approach is to calculate the curve horsepower that will
allow for the actual gear ratio and approximate density.
We are looking for a fan that at least will be an adequate
replacement for the original fan. Selecting a Hudson
fan to replace an existing fan is generally very simple.
The factors that must be known when replacing a fan
on an existing installation are:
- Fan diameter.
- Installed motor horsepower.
- Gear reduction ratio of
gear reducer.
- Shaft size or gear reducer
model.
- Some estimate of elevation
above sea level of installation.
2) Fan Selection
In selecting an optimum diameter
of fan, number of fan blades, type of blades, required
pitch angle, fan speed, and some estimate of horsepower
via the computer aid fan model selection program the
following factors should be considered and provided.
(1)Fan Use : Induced or Forced
Draft Cooling Tower
(2)Airflow Volume (acfm): A typical airflow volume by
the diameter of fan is as below. The normal air velocity
at fan inlet is 1,600 to 2,000 fpm and the air velocity
must not exceed 2,100 fpm. This is a guide line for
the optimum performance of fan. Excessive airflow may
result in a waste of horsepower and in a high drift
loss of water droplets through the fan cylinder.
Fan
Dia. (ft)
|
Net
Fan Area (ft2)
|
Normal Airflow (cfm)
|
Maximum
Airflow (cfm)
|
12
|
102.30
|
163,700 - 204,600
|
214,800
|
13
|
121.93
|
195,100 - 243,900
|
256,100
|
14
|
143.14
|
229,000 - 286,300
|
300,600
|
16
|
178.72
|
286,000 - 357,400
|
375,300
|
18
|
232.13
|
371,400 - 464,300
|
487,500
|
20
|
291.82
|
466,900 - 583,600
|
612,800
|
22
|
348.63
|
557,800 - 697,300
|
732,100
|
24
|
420.89
|
673,400 - 841,800
|
883,900
|
26
|
488.69
|
781,900 - 977,400
|
1,026,300
|
28
|
573.52
|
917,600 - 1,147000
|
1,204,400
|
30
|
654.62
|
1,063,400 - 1,329,200
|
1,395,700
|
(3) Diameter of Fan (ft)
or Cross Sectional Area of Tower (ft2): The
fan diameter has significant bearing on performance
primarily because the diameter effects the magnitude
of the velocity pressure which is a parasitic loss and
the fan diameter effects the pressure capability of
the fan. In our estimation, velocity pressure should
fall in the range of 0.14 to 0.25 inch water (1,600
to 2,000 fpm at 0.068 lb/ft3) for optimum
performance. Of course, other factors influence the
choice of fan diameter, such as cell-size limitations,
or selection of a fan for an existing installation.
Coping with a high velocity
pressure requirement is just to add blades. However,
this presents a good case for converting velocity pressure
into useful static pressure capability by adding velocity
recovery stack (called fan stack). The solidity ratio
expressed by the ratio of the total width of the fan
blades to the fan circumference is a way to compare
a fan's pressure capability. The higher the ratio, usually
the more work the fan can do. Still another aspect of
optimum fan diameter is cost. Nonstandard sizes mean
special handling by the fan maker at additional cost.
(Standard fan diameter: 7, 8, 9, 10, 11, 12, 13, 14,
16, 18, 20, 22, 24, 26, 28, 30, 32 in feet)
For a proper air distribution
the area of fan coverage shall not be less than 30%
of the cross sectional area of tower for the induced
draft type of cooling tower and 40% for the forced draft
type of cooling tower. Less fan diameter than these
percentages will require more plenum chamber for enough
mixing of air induced from the eliminators. Otherwise,
the poor mixed air will generate the air turbulence,
will make more vibration & noise, and will reduce
the fan performance. Of course, the air will not be
smoothly and evenly introduced into the fan from the
drift eliminator.
(4) Actual Static Pressure
(inch water): The total static pressure consists of
pressure drops at the air inlet & louver, the fill,
the eliminator, and the fan inlet. The pressure gain
using the velocity recovery fan stack can be deducted
from the total static pressure if you are using the
different type of velocity recovery defined in Chapter
4 (Fan Stack, 7?of incline, 70% of efficiency,
0.08% of tip clearance, inlet shape of elliptic).
The calculation of pressure
drops at the air inlet & louver, eliminator and
fan inlet are so easy, while the pressure drop at fill
can be read from the pressure drop curve (It depends
on the air velocity, water loading, depth of fill and
density of air, etc. with a specific model of fill.)
The pressure drops at the air inlet & louver, eliminator
and fan inlet can be generally obtained from a formula
of K x 1/2 x (density x 0.1922) x (V2/115,820),
where K is a pressure drop coefficient, 1g = 9.8016
m/sec2 = 115,820 ft/min2, and
1 lb/ft2 = 0.1922 inch H2O, whose
K is in general 1.5 to 3.5 for the air inlet & louver,
2.0 to 3.0 for eliminator, and 0.1 to 0.35 for the fan
inlet.
Pressure
Drop Coefficients
|
Location
|
Counter
Flow Type
|
Cross
Flow Type
|
Air
Inlet w/out Louver
|
1.5
|
N/A
|
Air
Inlet w/Large, widely spaced Louver
|
2
to 3
|
2
to 3
|
Air
Inlet w/Small, narrow spaced Louver
|
2.5
to 3.5
|
2.5
to 3.5
|
Eliminator
|
2.0
to 3.0
|
2.0
to 3.0
|
Fan
Inlet
|
0.1
to 0.35
|
0.1
to 0.35
|
(5) Temperature at Fan (oF)
& Elevation of Site (ft) or Air Density (lb/ft3):
This factor is very important in selecting the fans
because of their effect on fan pressure capability and
horsepower requirement through change in air density.
This factor is combined into a density ratio. Hudson
fan curve has a monograph for the density of dry air
at 70? and sea level. The exit air of wet cooling tower
is not simply a saturated air, but saturated air plus
water vapor.
(6) Type of Fan Inlet Shape:
Elliptical Inlet Bell (H/L = 0.15 x dia. of fan / 0.1
x dia. of fan) or what? Elliptical inlet shape proves
to be ideal because the air flows along the wall with
a uniform velocity and to the fan with the slightest
possible turbulence. Other inlet shapes may be considered
to add the extra resistance to the required duty point
of the fan. The extra resistance may be determined with
the aid of pressure loss factor. Also, the inlet shape
influences the sound production of the fans.
(7) Venturi Height (ft) from
Fan Plane to Top of Fan Stack : In the case of Wet Cooling
Towers, a relatively common means of improving inlet
conditions, conserving horsepower, and reducing the
air recirculation into the air inlet is known as a fan
stack. These stacks incorporate a slightly tapered exit
cone and a well rounded inlet bell. In theory, there
is a significantly reduced velocity pressure at the
exit compared to the plane of the fan. Since the quantity
of air is the same at both planes, the recovery of velocity
pressure is converted into "static regain"
which lowers the total pressure requirements of the
fan, thus saving horse power. Below is a general shape
of fan stack and is applicable for the actual cooling
tower.
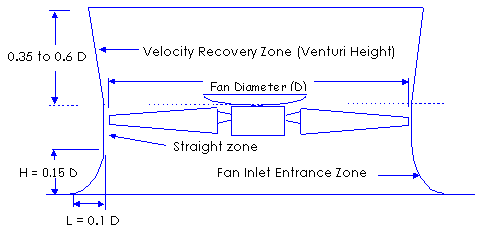
(8) Obstacle Area and Distance
from Fan: (ft2/ft): The obstacles are mostly
constituted by supporting beams, a gear reducer, and
drive shaft, etc. These interference in the air flow
due to obstacles located in the front of fan. Also,
these obstacles cause a partial obstruction of the cross
sectional area. As a result, extra losses occur. The
losses depend on the ratio of total cross sectional
area of fan casing to the obstacle area, and the ratio
of the fan casing diameter to the distance from obstacles
to the fan blade tip. Apart from a resistance increase
in the air flow, obstacles cause an increase in sound
production.
(9) Fan Speed (rpm), or motor
full load speed & gear reduction ratio
(10) Fan Driver: Electric
motor, speed control (single speed, two speed, or variable
speed)
(11) Blade Pitch Control:
Adjustable or variable pitch
(12) Number of Support Beam
(13) Minimum RF Margin (%):
Details are described in Chapter 5.
(14) Required Noise Level
(dB(A))
(15) Materials Construction
of Tower Structure and Fan Stack: This is to be considered
a maximum limit on the gear reducer itself not a normal
level. Common practice in US is to use the minimum number
of blades to reduce the vibration in the wood structure
tower and FRP fan stack. This is to avoid dangerous
air load induced pulsations on the fan cylinder. The
fewer blades are occurring the higher air loads and
are enlarging the more intense blade passing pulsation.
Minimum Number of Fan
Blades
|
Tower
Structure Materials
|
Fan
Stack Materials
|
Fan
Diameter (feet)
|
Min.
No. of Blades (Max. 80m
@ Gear)
|
Min.
No. of Blades (Max. 40m
@ Gear)
|
Concrete
|
Concrete/FRP
|
7
- 14
|
4
each
|
5
each
|
16
- 20
|
4
each
|
6
each
|
22
- 32
|
6
each
|
8
each
|
Woods or Steel
|
FRP
|
7
- 14
|
5
each
|
6
- 8 each
|
16
- 20
|
6
each
|
8
- 10 each
|
22
- 32
|
8
each
|
10
- 12 each
|
As a general rule, do not
select the fans close to the limit of their BHP/blade.
As bhp per blade = Brake Horse Power / Number of Blade,
high blade air loading result in fatigue, vibration
and noise problems. So, Hudson recommends the maximum
per blade to be able to allow for fans as follows and
4 hp or less per blade is trouble free in most applications.
These are guide line only and the minimum number of
blades per fan would also be influenced by fan ring
or fan stack rigidity or unusual loading conditions.
If the bhp/blade is excessive, you may:
- Increase the number of
blades specified.
- Increase the fan diameter.
- Change to a wider chord
blade type, if possible.
- Decrease the static pressure,
if possible.
Fan Diameter
|
Maximum BHP/Blade
|
Trouble Free BHP/Blade
|
H
Type
|
HW
Type
|
H
Type
|
HW
Type
|
12
ft
|
8.0
HP
|
10.0
HP
|
4.0
HP
|
6.0
HP
|
13
ft
|
9.0
HP
|
11.25
HP
|
5.0
HP
|
7.25
HP
|
14
ft
|
10.0
HP
|
12.5
HP
|
6.0
HP
|
8.5
HP
|
15
ft
|
11.0
HP
|
|
7.0
HP
|
|
16
ft
|
12.0
HP
|
|
8.0
HP
|
|
18
ft
|
14.0
HP
|
|
10.0
HP
|
|
20
ft
|
16.0
HP
|
|
12.0
HP
|
|
22
ft
|
18.0
HP
|
|
14.0
HP
|
|
24
ft
|
20.0
HP
|
|
16.0
HP
|
|
26
ft
|
22.0
HP
|
|
18.0
HP
|
|
28
ft
|
24.0
HP
|
|
20.0
HP
|
|
30
ft
|
26.0
HP
|
|
22.0
HP
|
|
32
ft
|
28.0
HP
|
|
24.0
HP
|
|
|